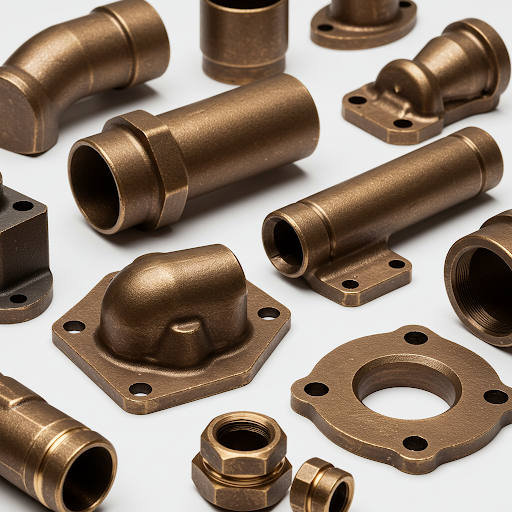
High quality Casting from A1Metallics- Bronze Casting, Gunmetal casting, Lg2 casting, Bronze casting Foundry
Premium Bronze Casting Solutions
We are one of the leading manufacturers and exporters of high-quality Bronze, Gunmetal, and special Bronze alloy castings from India. We have been supplying premium Bronze castings to the world market for many decades. Our state-of-the-art foundry specializes in producing precise and durable castings that meet international standards and specifications. With our advanced machinery, skilled workforce, and commitment to excellence, we have established ourselves as a trusted partner for industries across the globe. Our Bronze casting solutions are known for their superior quality, dimensional accuracy, excellent surface finish, and consistent metallurgical properties. We pride ourselves on delivering customized solutions tailored to meet specific requirements of our clients while maintaining competitive pricing and timely delivery.
Bronze Casting
Overview
Bronze casting is a sophisticated metal forming process that involves melting Bronze alloys and pouring them into prepared molds to create components with specific shapes and properties. Our Bronze castings are known for their excellent corrosion resistance, high tensile strength, and superior wear resistance. We utilize both sand casting and investment casting techniques to produce components ranging from small intricate parts to large industrial components weighing up to 500 kg.
Material Grades
Our Bronze castings are available in various grades to suit different application requirements:
| Grade | Composition | Properties | Applications |
|--------|-----------------------------------|---------------------------------------------------------|--------------------------------------|
| C90300 | Copper 88%, Tin 8%, Zinc 4% | Excellent corrosion resistance, good mechanical properties | Marine hardware, pumps, valves |
| C90500 | Copper 88%, Tin 10%, Zinc 2% | Superior strength, high corrosion resistance | Bearings, bushings, gears |
| C90700 | Copper 89%, Tin 11% | Exceptional corrosion resistance in seawater | Marine components, pump impellers |
| C91100 | Copper 84%, Tin 16% | High hardness, excellent wear resistance | Heavy-duty bearings, worm gears |
| C92200 | Copper 86%, Tin 6%, Zinc 4%, Lead 4% | Good machinability, pressure tightness | Valve bodies, pump components |
Manufacturing Processes
Our Bronze casting manufacturing process includes:
- Pattern Making: Creation of precise patterns based on engineering drawings
- Mold Preparation: Using high-quality sand molds or investment casting shells
- Melting: Utilizing induction furnaces for precise temperature control
- Pouring: Controlled pouring to minimize defects
- Cooling and Solidification: Carefully monitored to ensure proper grain structure
- Shakeout: Removal of casting from the mold
- Fettling and Cleaning: Removal of gates, risers, and excess material
- Heat Treatment: To achieve desired mechanical properties
- Machining: Precision machining to achieve tight tolerances
- Quality Inspection: Dimensional checks, material testing, and NDT
Machinery Used
Our foundry is equipped with modern machinery to ensure high-quality castings:
- Medium frequency induction melting furnaces (capacity: 100-500 kg)
- Automatic sand mixers and molding machines
- Shell molding equipment
- Investment casting furnaces
- CNC machining centers
- Coordinate measuring machines (CMM)
- Spectroscopic analysis equipment
- Mechanical testing laboratory
Typical Parts Produced
Bronze castings are widely used for manufacturing:
- Pump components (impellers, casings, diffusers)
- Valve bodies and components
- Marine hardware and fittings
- Bushings and bearings
- Gears and gear blanks
- Propellers and propeller components
- Ornamental and architectural elements
Dimensional Chart for Standard Bronze Bushings
Inner Diameter (mm)Outer Diameter (mm)Length (mm)Wall Thickness (mm)101520-502.5152225-603.5202830-804.0253540-1005.0304250-1206.0405560-1507.5507075-20010.075100100-25012.5100130120-30015.0
Surface Finish
We offer various surface finishes for our Bronze castings:
- As-cast (Ra 12.5-25 μm)
- Sand blasted (Ra 6.3-12.5 μm)
- Machined (Ra 1.6-3.2 μm)
- Polished (Ra 0.8-1.6 μm)
- Mirror polished (Ra <0.8 μm)
Industries Served
Our Bronze castings are used in numerous industries:
- Marine and shipbuilding
- Oil and gas
- Water and wastewater treatment
- Chemical processing
- Power generation
- Mining and minerals processing
- Pulp and paper
- Food processing
- Architectural and ornamental
Tolerances
Our Bronze castings conform to the following dimensional tolerances:
- Sand casting: ±0.5 mm per 100 mm
- Investment casting: ±0.2 mm per 100 mm
- Machined components: ±0.05 mm
Turnaround Time
Standard turnaround time for our Bronze castings is 4-6 weeks from order confirmation to dispatch. For urgent requirements, expedited production can be arranged upon request.
Gunmetal Casting
Overview
Gunmetal is a type of Bronze containing Copper, Tin, and Zinc that offers exceptional corrosion resistance, especially in marine environments. Our Gunmetal castings are renowned for their excellent mechanical properties, machinability, and pressure tightness. We specialize in producing high-quality Gunmetal castings for applications requiring superior performance in demanding conditions.
Material Grades
We produce Gunmetal castings in the following grades:
GradeCompositionPropertiesTypical ApplicationsG1 (LG1)Cu 85%, Sn 5%, Zn 5%, Pb 5%Excellent pressure tightness, good machinabilityValve bodies, pump casingsG2 (LG2)Cu 87%, Sn 10%, Zn 3%Superior corrosion resistance, high strengthMarine fittings, propellersG3 (LG3)Cu 85%, Sn 11%, Zn 4%High tensile strength, excellent wear resistanceGears, bushings, bearingsG4 (LG4)Cu 86%, Sn 7%, Zn 7%Good casting properties, moderate strengthGeneral engineering components
Manufacturing Processes
Our Gunmetal casting process involves:
- Material Selection: Careful selection and testing of raw materials
- Melting: Using medium frequency induction furnaces for precise composition control
- Mold Preparation: Using high-quality silica sand with appropriate binders
- Pouring: Temperature-controlled pouring for optimal grain structure
- Cooling and Solidification: Carefully monitored cooling cycles
- Finishing: Fettling, shot blasting, and machining as required
- Quality Control: Chemical analysis, mechanical testing, and dimensional verification
Machinery Used
Our Gunmetal casting facility includes:
- Medium frequency induction melting furnaces
- Automatic sand mixers and molding machines
- Vertical and horizontal CNC machining centers
- Sand blasting equipment
- Material testing laboratory
- 3D scanning and inspection systems
Typical Parts Produced
Common Gunmetal castings include:
- Valve bodies and components
- Pump casings and impellers
- Marine hardware and fittings
- Propellers and propeller components
- Gears and gear blanks
- Bushings and bearings
- Steam fittings and components
Performance Metrics
Typical performance characteristics of our Gunmetal castings:
PropertyValue RangeTensile Strength220-320 MPaYield Strength110-170 MPaElongation10-20%Hardness60-90 HBDensity8.7-8.9 g/cm³Maximum Working Temperature200-260°CCorrosion ResistanceExcellent (particularly in seawater)Wear ResistanceGood to ExcellentMachinability70-90% (compared to free-cutting Brass)
Industries Served
Gunmetal castings are widely used in:
- Marine engineering
- Oil and gas
- Power generation
- Water treatment
- Chemical processing
- Food processing
- General engineering
Tolerances
Our Gunmetal castings meet the following tolerances:
- As-cast: ±0.5 mm per 100 mm
- Machined: ±0.05 mm
Turnaround Time
Standard production time for Gunmetal castings is 4-6 weeks. Rush orders can be accommodated based on production capacity.
LG2 Bronze Casting
Overview
LG2 Bronze (also known as Phosphor Bronze or Gunmetal G2) is a high-quality alloy comprising approximately 87% Copper, 10% Tin, and 3% Zinc. Our LG2 Bronze castings are highly regarded for their exceptional corrosion resistance, particularly in marine environments, excellent mechanical properties, and superior pressure tightness. We specialize in precision LG2 castings for applications where reliability and longevity are paramount.
Material Properties
LG2 Bronze offers an excellent combination of properties:
PropertyValueTensile Strength280-320 MPaYield Strength140-160 MPaElongation15-20%Hardness75-85 HBDensity8.8 g/cm³Melting Range880-980°CThermal Conductivity59 W/m·KElectrical Conductivity12% IACSCoefficient of Thermal Expansion18.0 × 10⁻⁶/°C
International Standards
LG2 Bronze conforms to various international standards:
- BS 1400 LG2
- ASTM B584 C90500
- DIN 1705 G-CuSn10Zn
- ISO 1338 CuSn10Zn
- JIS H5120 CAC502
Manufacturing Processes
Our LG2 Bronze casting process includes:
- Material Preparation: Careful selection and analysis of raw materials
- Melting: Controlled melting in induction furnaces with precise temperature monitoring
- Pouring: Carefully controlled pouring to minimize defects
- Solidification: Monitored cooling for optimal grain structure
- Fettling: Removal of gates, risers, and excess material
- Heat Treatment: When required for specific properties
- Machining: Precision machining to achieve tight tolerances
- Quality Control: Comprehensive testing and inspection
Typical Applications
LG2 Bronze castings are commonly used for:
- Marine propellers and propeller components
- Ship fittings and hardware
- Valve bodies and components
- Pump casings and impellers
- Gears and gear wheels
- Bushings and bearings for heavy-duty applications
- Steam and water fittings
- Architectural components requiring durability and aesthetics
Dimensional Table for Standard LG2 Bronze Valve Bodies
Nominal Size (inches)Body Length (mm)Body Width (mm)Body Height (mm)Wall Thickness (mm)1/2"75506063/4"90607071"100708081.5"120859592"140100110103"180130140124"220160170146"28021022016
Industries Served
LG2 Bronze castings are extensively used in:
- Marine and shipbuilding
- Oil and gas
- Power generation
- Water treatment
- Chemical processing
- Mining and minerals processing
- Pulp and paper
Tolerances
Our LG2 Bronze castings meet the following tolerances:
- Sand casting: ±0.5 mm per 100 mm
- Investment casting: ±0.2 mm per 100 mm
- Machined components: ±0.05 mm
Turnaround Time
Standard turnaround time for LG2 Bronze castings is 4-6 weeks from order confirmation to dispatch.
Bronze Casting Foundry
Overview
Our state-of-the-art Bronze casting foundry is equipped with advanced machinery and operated by skilled technicians with decades of experience. We specialize in producing high-quality castings in various Bronze alloys, including Tin Bronze, Aluminum Bronze, Phosphor Bronze, Gunmetal, and Silicon Bronze. Our foundry capabilities include sand casting, investment casting, and centrifugal casting processes to meet diverse requirements.
Foundry Capabilities
ParameterSpecificationMelting Capacity100-1000 kg per heatCasting Weight Range0.5-500 kgAnnual Production Capacity1000 tonsMold TypesGreen sand, CO₂, shell, investmentPattern MaterialsWood, aluminum, resin, 3D printedMaterial TestingSpectrographic analysis, mechanical testing, NDTQuality ControlIn-process inspections, final inspection, documentation
Production Facilities
Our foundry includes:
- Medium frequency induction melting furnaces
- Electric resistance furnaces for heat treatment
- Automatic and semi-automatic molding lines
- Core making machines
- Sand preparation and reclamation systems
- Shot blasting equipment
- Fettling and finishing stations
- Machining department with CNC capabilities
- Inspection and testing laboratory
Quality Assurance
Our quality assurance system includes:
- Material certification and traceability
- In-process quality checks
- Final inspection and testing
- Documentation and record-keeping
- Product marking and identification
- Customer-specific quality requirements
Testing Capabilities
Our foundry laboratory is equipped to perform:
- Chemical composition analysis
- Mechanical property testing (tensile, yield, elongation)
- Hardness testing
- Microstructure analysis
- Non-destructive testing (radiography, ultrasonic, magnetic particle, dye penetrant)
- Pressure testing for valves and pump components
C836 Bronze Casting
Overview
C836 Bronze (also known as Aluminum Bronze) is a specialized Bronze alloy containing approximately 83% Copper, 11% Aluminum, 4% Iron, and 2% Nickel. Our C836 Bronze castings offer exceptional strength, hardness, and wear resistance combined with excellent corrosion resistance, particularly in marine environments. This premium alloy is ideal for high-stress applications where durability and reliability are essential.
Material Properties
C836 Aluminum Bronze offers superior mechanical properties:
PropertyValueTensile Strength580-650 MPaYield Strength250-300 MPaElongation12-18%Hardness150-180 HBDensity7.6 g/cm³Melting Range1030-1080°CThermal Conductivity42 W/m·KElectrical Conductivity7% IACSMaximum Service Temperature400°C
International Standards
C836 Bronze conforms to:
- ASTM B148 C95800
- BS 1400 AB2
- DIN 1714 CuAl10Fe5Ni5
- ISO 428 CuAl10Fe5Ni5
- JIS H5202 CAC703
Manufacturing Processes
Our C836 Bronze casting process includes:
- Material Preparation: Careful selection and testing of raw materials
- Melting: Using induction furnaces with precise temperature control
- Degassing and Deoxidation: Special treatments to ensure casting quality
- Pouring: Controlled pouring under protective atmosphere
- Solidification: Carefully monitored cooling cycles
- Heat Treatment: To achieve optimal mechanical properties
- Machining: High-precision machining with specialized tooling
- Quality Control: Comprehensive testing and inspection
Typical Applications
C836 Bronze castings are commonly used for:
- Marine propellers for high-performance vessels
- Pump impellers for corrosive environments
- Valve components for high-pressure applications
- Bearings and bushings for heavy loads
- Gears for high-stress applications
- Oil and gas industry components
- Chemical processing equipment
Industries Served
C836 Bronze castings are extensively used in:
- Marine and shipbuilding
- Oil and gas
- Mining and minerals processing
- Chemical processing
- Power generation
- Aerospace
- Defense
Tolerances
Our C836 Bronze castings meet the following tolerances:
- Sand casting: ±0.5 mm per 100 mm
- Investment casting: ±0.2 mm per 100 mm
- Machined components: ±0.05 mm
Turnaround Time
Standard turnaround time for C836 Bronze castings is 4-6 weeks from order confirmation to dispatch.
Gunmetal Casting
Overview
Gunmetal is a type of Bronze containing Copper, Tin, and Zinc that offers exceptional corrosion resistance, especially in marine environments. Our Gunmetal castings are renowned for their excellent mechanical properties, machinability, and pressure tightness. We specialize in producing high-quality Gunmetal castings for applications requiring superior performance in demanding conditions.
Gunmetal casting represents one of our core competencies, with our foundry producing precision components using both traditional and advanced casting techniques. The superior metallurgical properties of Gunmetal make it indispensable for applications where resistance to wear, corrosion, and fatigue are paramount. Our metallurgists carefully control the melting and alloying process to ensure optimal microstructure development, resulting in castings with excellent mechanical integrity and consistent properties throughout the component. We employ advanced simulation software to optimize gating and risering systems, minimizing porosity and ensuring complete mold filling. This technological approach, combined with our decades of hands-on experience, enables us to produce Gunmetal castings that exceed industry standards for dimensional accuracy and material performance.
Gunmetal Fittings
Our Gunmetal fittings represent the pinnacle of precision engineering and metallurgical excellence. These components are specifically designed for applications requiring superior sealing properties, pressure resistance, and longevity in challenging environments. We manufacture a comprehensive range of Gunmetal fittings including pipe fittings, flanges, valve bodies, pump connectors, and specialized marine components. Each fitting undergoes rigorous hydrostatic pressure testing to ensure absolute leak-free performance under operational conditions. Our Gunmetal fittings are particularly valued in marine engineering, where their exceptional resistance to dezincification and stress corrosion cracking in seawater environments makes them irreplaceable for critical systems. The superior machinability of our Gunmetal alloys allows us to produce fittings with intricate threading, precise dimensions, and excellent surface finishes. All our Gunmetal fittings comply with international standards including BS 1400, ASTM B62, and JIS H5120, ensuring global compatibility and interchangeability.
Grades:
G1 (LG1) – Cu 85%, Sn 5%, Zn 5%, Pb 5% – Excellent pressure tightness, good machinability – Valve bodies, pump casings
G2 (LG2) – Cu 87%, Sn 10%, Zn 3% – Superior corrosion resistance, high strength – Marine fittings, propellers
G3 (LG3) – Cu 85%, Sn 11%, Zn 4% – High tensile strength, excellent wear resistance – Gears, bushings, bearings
G4 (LG4) – Cu 86%, Sn 7%, Zn 7% – Good casting properties, moderate strength – General engineering components
Why Choose Our Bronze Castings?
Our Bronze casting solutions offer numerous advantages:
Superior Quality
We maintain rigorous quality control throughout our production process, ensuring castings with excellent mechanical properties, dimensional accuracy, and surface finish. Our foundry is ISO 9001:2015 certified, guaranteeing consistent quality across all products.
Technical Expertise
With over three decades of experience in Bronze casting, our team possesses deep technical knowledge and expertise in metallurgy, casting design, and manufacturing processes. We provide valuable technical input during the product development phase to optimize designs for manufacturability and performance.
Customization Capabilities
We offer extensive customization options to meet specific requirements:
- Custom alloy compositions
- Special mechanical properties through heat treatment
- Tailored surface finishes
- Precision machining to tight tolerances
- Custom packaging with customer labels/logos
Global Experience
Having served customers across North America, Europe, Asia, and Australia for over three decades, we understand international quality standards and business practices. Our export expertise ensures smooth transactions and reliable delivery regardless of destination.
Competitive Pricing
Our efficient production processes, combined with the advantages of manufacturing in India, allow us to offer highly competitive pricing without compromising on quality.
Excellent Communication
Our customer service team is fluent in English and available around the clock to accommodate different time zones. We provide regular updates on production status and respond promptly to queries and concerns.
Reliable Delivery
We maintain strict production schedules to ensure on-time delivery. Our established relationships with freight forwarders and shipping companies enable efficient logistics management for international shipments.
Packaging and Shipping
We take utmost care in packaging our Bronze castings to ensure they reach you in perfect condition:
Standard Packaging
- Individual components wrapped in VCI paper for corrosion protection
- Secure placement in wooden crates or pallets with adequate cushioning
- Weather-resistant covering
- Clear marking and labeling
Customized Packaging
- Customer-specific packaging requirements
- Custom labels with customer logo and part numbers
- Special corrosion protection for long-term storage
- Documentation as per customer specifications
Shipping Options
- Air freight for urgent deliveries
- Sea freight for larger consignments
- Door-to-door delivery through trusted logistics partners
- Export documentation and customs clearance assistance
Frequently Asked Questions
Q: What is the minimum order quantity for Bronze castings? A: Our minimum order quantity is typically 10 pieces for standard components. For custom designs, the minimum quantity may vary depending on complexity and size.
Q: Can you produce castings based on our drawings? A: Yes, we can manufacture castings based on your drawings or specifications. We can work with various file formats including DWG, DXF, STEP, and PDF.
Q: What quality certifications do you have? A: Our foundry is ISO 9001:2015 certified. We can also provide material test certificates as per EN 10204 3.1 or 3.2 if required.
Q: Do you provide samples before bulk production? A: Yes, we can provide sample castings for approval before proceeding with bulk production. Sample costs depend on the complexity and size of the component.
Q: What is your typical lead time for Bronze castings? A: Our standard lead time is 4-6 weeks from order confirmation. For urgent requirements, we can offer expedited production at an additional cost.
Q: Can you perform machining operations on the castings? A: Yes, we have in-house machining capabilities to provide fully machined components as per your specifications.
Q: What testing do you perform on your castings? A: We perform chemical analysis, mechanical testing (tensile, hardness), dimensional inspection, and NDT as required. Additional testing can be arranged upon request.
Q: How do you handle design changes after order placement? A: Design changes can be accommodated depending on the production stage. Changes made after pattern production or during casting production may incur additional costs and affect delivery timelines.
Q: What payment terms do you offer? A: Our standard payment terms are 50% advance with order and 50% before shipment. For established customers, we can offer more flexible payment terms.
Q: Do you provide warranty for your castings? A: Yes, we provide a warranty against manufacturing defects for a period of 12 months from the date of delivery.
Glossary of Terms
Alloy: A mixture of metals or a metal combined with one or more other elements.
Bronze: An alloy consisting primarily of Copper with additions of other elements, most commonly Tin.
Casting: A manufacturing process in which a liquid material is poured into a mold containing a hollow cavity of the desired shape and allowed to solidify.
Corrosion Resistance: The ability of a material to withstand degradation due to reactions with its environment.
Fettling: The process of removing excess material from a casting, such as gates, risers, and flash.
Gunmetal: A type of Bronze containing Copper, Tin, and Zinc that offers good corrosion resistance and casting properties.
Investment Casting: A precision casting process that employs a wax pattern encased in a ceramic shell.
LG2: A specific grade of Gunmetal Bronze containing approximately 87% Copper, 10% Tin, and 3% Zinc.
Machinability: The ease with which a material can be cut (machined) to achieve the desired shape, size, and finish.
Non-Destructive Testing (NDT): Methods of testing that do not damage the tested component, such as radiography, ultrasonic testing, and dye penetrant inspection.
Phosphor Bronze: A Bronze alloy containing Phosphorus as a deoxidizer, offering improved strength and spring qualities.
Sand Casting: A casting process where molten metal is poured into a sand mold.
Tensile Strength: The maximum stress a material can withstand while being stretched before breaking.
Related Terms
- Bronze Bushings Manufacturer
- Marine Bronze Castings
- Phosphor Bronze Castings
- Aluminum Bronze Components
- Bronze Valve Body Suppliers
- Gunmetal Castings for Marine Applications
- LG2 Bronze Pump Components
- C836 Bronze Propeller Manufacturer
- High-Quality Bronze Investment Casting
- Bronze Sand Casting Services
- Bronze Alloy Engineering Components
- Custom Bronze Casting Solutions
- Bronze Casting for Industrial Applications
- Corrosion-Resistant Bronze Components
- Bronze Casting Exporters India
- Bronze Green Sand Casting Bronze Parts Bronze Machined Casting Bronze Parts Bronze Components
- Bronze Shell Casting Bronze Shell Molding Transformer Spades, Transformer Spade Terminals, Bronze Transformer Spade Connectors , Bronze Spades , Bronze Spade Terminals for Transformers
- Hotline clamps Bronze , Silicon Bronze Casting , Silicon Bronze Casting Foundry Bronze Transformer Spades Spade Terminals Bronze Spades Eye Bolts Bronze Parts Bronze Machined Casting Bronze Parts Bronze Components
Customer Testimonial
“We have been sourcing Bronze valve components from this foundry for over five years now. Their quality is consistently excellent, and their technical team has been invaluable in helping us optimize our designs for better performance. Their communication is outstanding, and they’ve never missed a delivery deadline. I highly recommend them for any Bronze casting requirements.”
Robert Anderson, Chief Procurement Officer, , USA